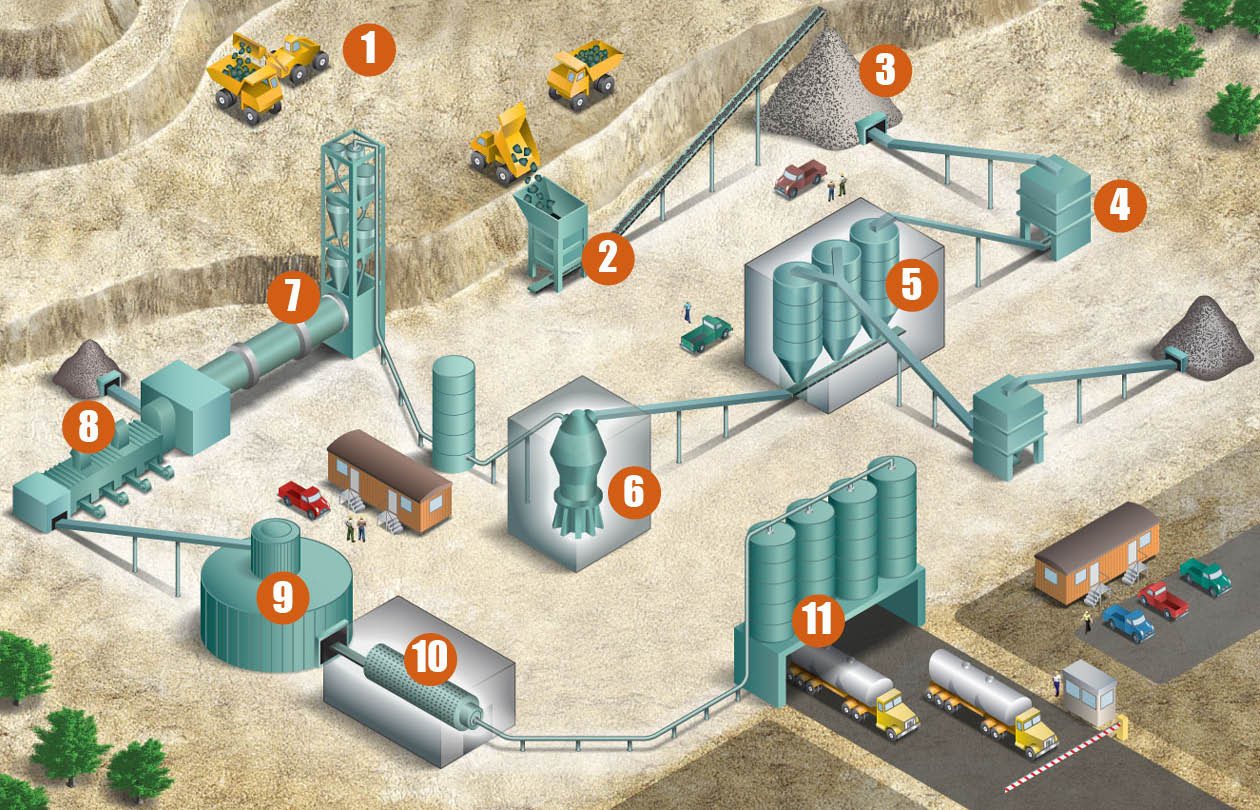
Cement Process Map
11.6.1 Process Description1-7 Portland cement is a fine powder, gray or white in color, that consists of a mixture of hydraulic cement materials comprising primarily calcium silicates, aluminates and aluminoferrites.
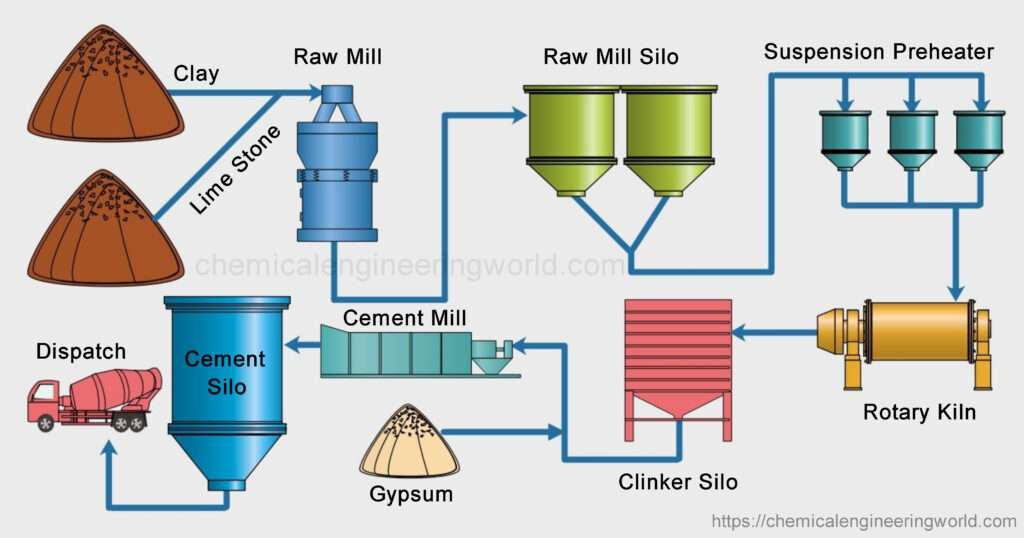
Cement Production Process Flow Diagram Photos
Process flow diagram for the cement manufacturing process, showing electricity and heat consumption or inputs [39]. Source publication Energy Savings Associated with the Use of Fly Ash and.

Chaeng new dry process cement prodution line(cement making process)
They are mixed either dry (dry mixing) or by water (wet mixing). 3) Prepared raw mix is fed into the rotary kiln. 4) As the materials pass through the kiln their temperature is rised upto 1300-1600 °C. The process of heating is named as "burning". The output is known as "clinker" which is 0.15-5 cm in diameter.
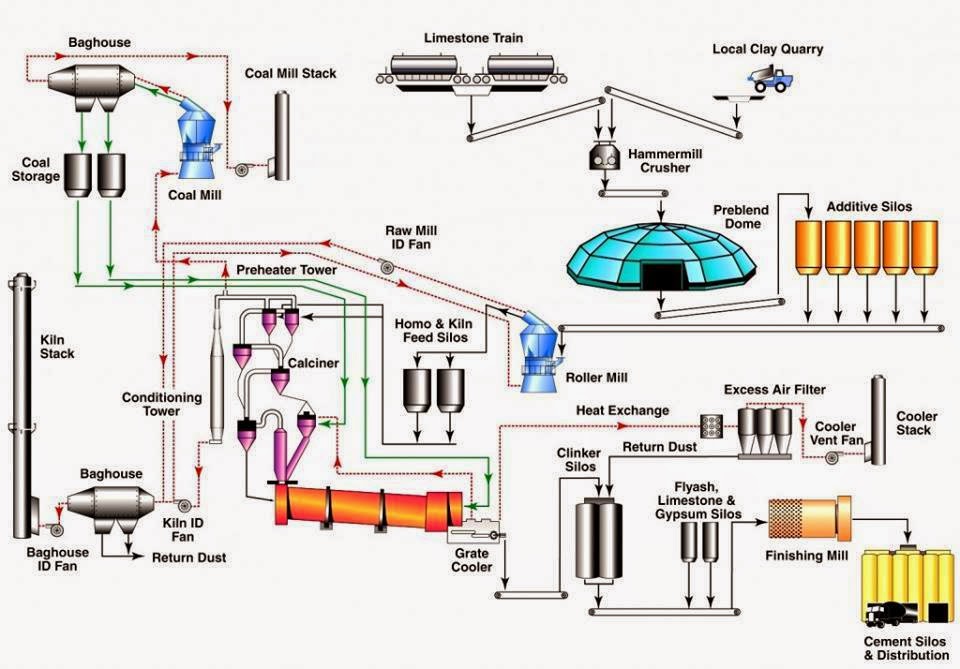
Chemical Engineering Information Flow Chart Of Cement Industry { Dry Process }
Cement making process Raw materials, clinker, cement Cement Chemist' Language CEMENT NOTATION IS A SHORT HAND WAY TO GIVE THE PHASE COMPOSITION OF A CEMENT IS BASED ON MODEL COMPOUNDS ACTUAL CEMENT PHASES ARE MORE OR LESS CLOSE TO THIS IDEAL VIEW CEMENT INDUSTRY SYMBOLS TYPICAL COMPOUND COMPOSITION OF ORDINARY PORTLAND CEMENT CHEMICAL NAME
DETAILED MANUFACTURING PROCESS OF CEMENT lceted LCETED INSTITUTE FOR CIVIL ENGINEERS
A cement process flow diagram (PFD) is a graphical representation of the main steps and equipment involved in producing cement from raw materials. It can help you understand how the process.

Cement Notes Class 12 Applied Chemistry Unit 19 NEB Notes
Cement Manufacturing Process Flowsheet (Flow Chart) Source publication Cement Manufacturing - Process Modeling and Techno-Economic Assessment (TEA) using SuperPro Designer. Preprint.

Process Flow Diagram of the Cement Plant Download Scientific Diagram
The following is a cement manufacturing process flow chart, cement manufacturing process flow chart. 5. As the per-flow diagram of the wet process of cement manufacturing, the rotary kiln is an essential and important component of a cement manufacturing factory. 6. It is made of a thick steel cylinder of diameter anything from 3 meters to 8.

Wet Process Of Cement Manufacturing With Flow Chart Civiconcepts
There are six main stages of the cement manufacturing process. Stage 1: Raw Material Extraction/Quarry The raw cement ingredients needed for cement production are limestone (calcium), sand and clay (silicon, aluminum, iron), shale, fly ash, mill scale, and bauxite. The ore rocks are quarried and crushed into smaller pieces of about 6 inches.
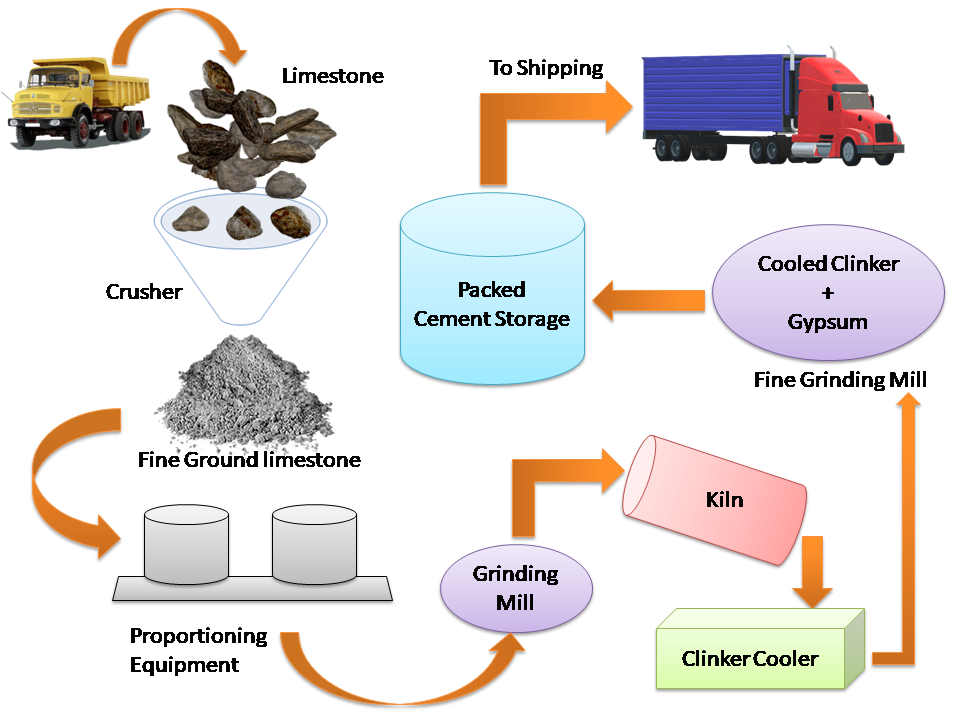
What is Cement and How it is Manufactured? The Machine Design
The flow diagram of mixing of raw materials by dry process. Flow diagram of dry process cement. Wet process ( old technology ) In the earlier part of the century i.e., from 1913 to 1960, the wet process was used for the manufacture of cement. From 1913 onwards, the cement industry underwent a number of changes mainly to suit the requirements of.
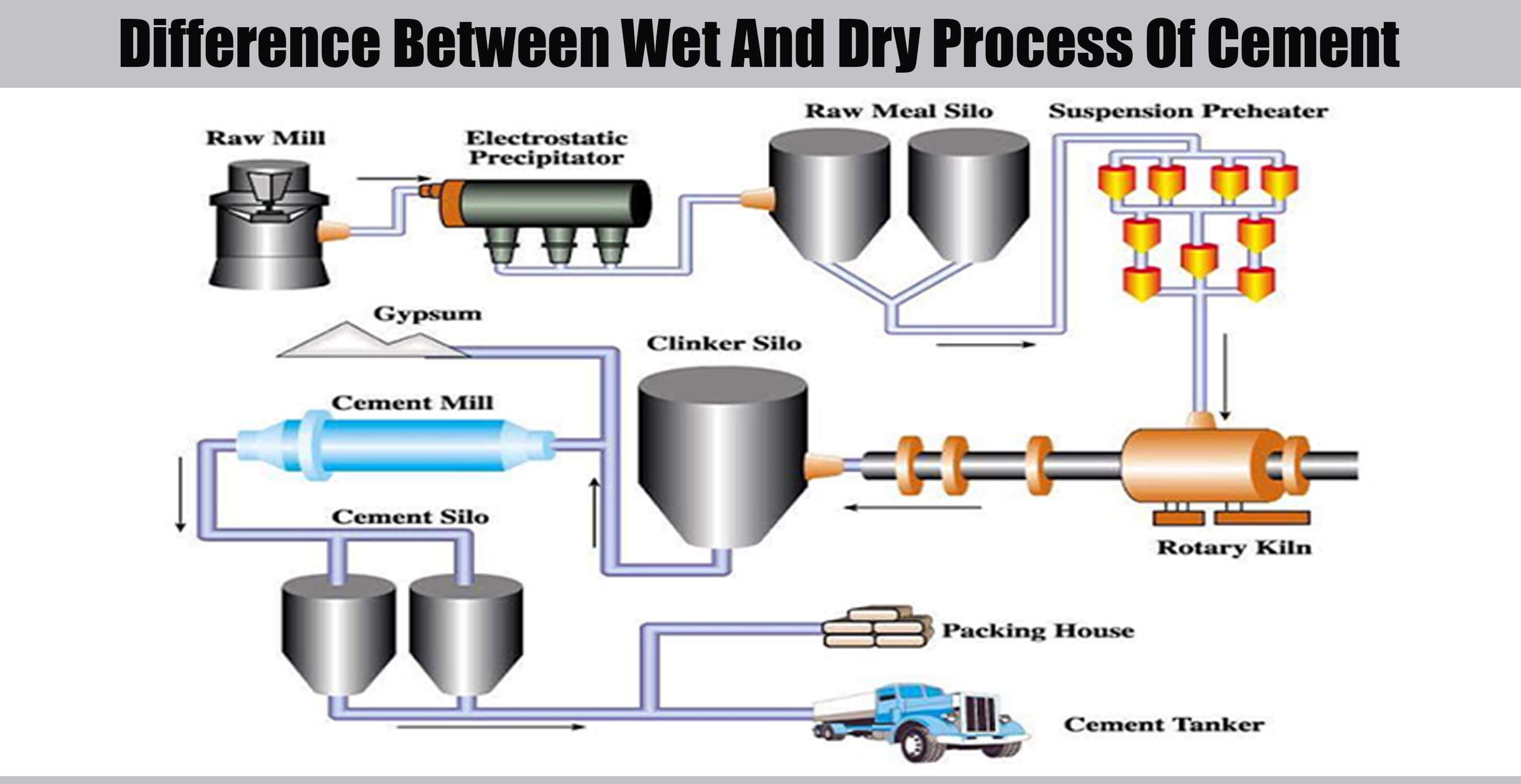
Difference Between Wet And Dry Process Of Cement Engineering Discoveries
A. Cement manufacturing Process Source:civilengineeringforum.me. As can be seen in Fig 1 (Process and Quality flow diagram) above, there are around 8 quality check points where by different samples are taken at some time interval (every hour most of the time) to check whether the raw materials/intermediate.
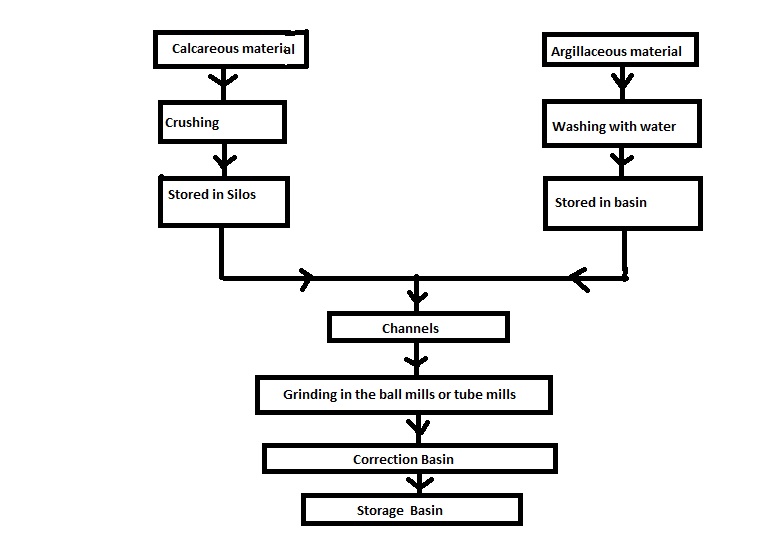
Civil Engineering materials. Wet process Cement manufacturing Flow Diagram
Cement Manufacturing Process Phase 1: Raw Material Extraction Cement uses raw materials that cover calcium, silicon, iron and aluminum. Such raw materials are limestone, clay and sand. Limestone is for calcium. It is combined with much smaller proportions of sand and clay. Sand & clay fulfill the need of silicon, iron and aluminum.

Manufacturing of Portland Cement Process and Materials Cement Concrete
Cement manufacturing is a complex process that begins with mining and then grinding raw materials that include limestone and clay, to a fine powder, called raw meal, which is then heated to a sintering temperature as high as 1450 °C in a cement kiln.

2 Process Of Manufacture Of Cement Wet Process & Dry Process Of Cement Manufacture Civil Giant
Cement Manufacturing Process Flow Chart (i) Drying Zones: In the wet process, the drying zone is comparatively larger than the dry process. It is because the raw material in slurry form is directly fed into the kiln which has more amount of water. As shown in the figure it is the upper portion of the kiln.
1 Simplified schematic flow chart of the dry process of manufacturing... Download Scientific
Context 1. 40% of the CO 2 comes from fossil fuel combustion in the kiln process, about 50% is due to de-carbonation of limestone (CaCO 3 ) to calcium oxide (CaO), and the remaining 10% is.
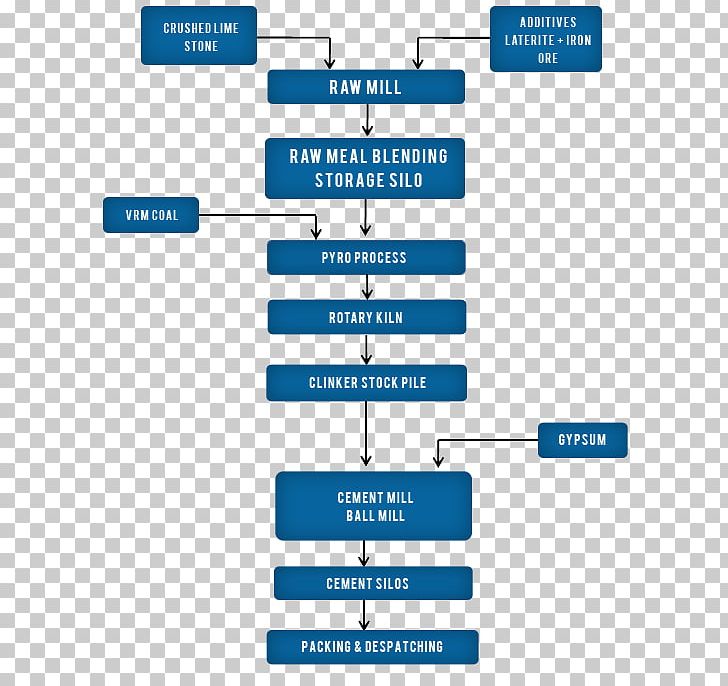
Portland Cement Flowchart Process Flow Diagram Manufacturing PNG, Clipart, Angle, Area, Brand
The Fig.1. show the flow diagram of the dry process of the manufacture of cement. 1. Dry Process. In the dry and semi-dry process the raw materials are crushed in a dry state. Then, they are processed in grinding mill, dried and reduced to very fine powder-like. That dry power is further blended, corrected for the right composition and mixed.

Cement Production Process Flow Diagram Photos
In this study the process flow diagram for the cement production was simulated using Aspen HYSYS 8.8 software to achieve high energy optimization and optimum cement flow rate by varying the flow rate of calcium oxide and silica in the clinker feed. Central composite Design (C.C.D) of Response Surface Methodology was used to design the ten experiments for the simulation using Design Expert 10.0.3.